Coiled tubing 825 chemical injection line welded coiled tubing
Description
Alloy 825 Coiled Capillary Tubing for Control Lines
A direct hydraulic control umbilical provides direct hydraulic control of each valve on a subsea christmas tree, through a bundle of tubes from the topsides hydraulic power unit (HPU) to the subsea tree. No electrical power or signal is required. Actuation of valves is by the supply of hydraulic power to the relevant tube. This is accomplished by opening the relevant valve on the manifold located on the topsided HPU. This type of umbilical is limited to subsea production systems with short offsets to the host and few trees.
Thanks to the experience and expertise gained in the production and inspection, the tubes supplied by Meilong fully meet stringent quality requirements of the oil & gas industries. The tubing deployed in the umbilicals used in aggressive subsea and downhole conditions.
The molybdenum content present in the 825 coiled tubing aids in the alloy’s resistance to pitting and crevice corrosion as well. The chromium content in the Inconel 825 coiled tubing confers the alloy with resistance to various of oxidizing substances such as nitric acid, nitrates and to oxidizing salt. The titanium addition in 825 coiled tubing with an appropriate heat treatment, serves to stabilize the metal against sensitization to intergranular corrosion.
Therefore, material like the Inconel 825 coiled tubing , which has been furnished under the ASTM B423 specification needs to conform to the applicable requirements such as the chemical and mechanical specified herein. Properties like the materials Tensile strength, yield strength and elongation of the Inconel 825 coiled tubing under the specified condition and size of the Alloy 825 coiled tubing need to also conform to the required mechanical properties. Tests such as the Hydrostatic and non-destructive electric one need to be performed on the 825 coiled tubing In theory the pressure capability of tubing made by the welded and annealed method should be the same but it is common practice in design codes to down-rate welded tubing due to the risk of an imperfect weld leading to weakness. The strains involved in a following redrawing operation will establish the quality of the seam weld and any centre-line weakness will be exposed and detected by visual inspection and/or pressure testing. Therefore the seamless welded and sunk and welded & sunk/plug drawn tubes have the same pressure rating which is superior to that of welded tubing.
In theory the pressure capability of tubing made by the welded and annealed method should be the same but it is common practice in design codes to down-rate welded tubing due to the risk of an imperfect weld leading to weakness. The strains involved in a following redrawing operation will establish the quality of the seam weld and any centre-line weakness will be exposed and detected by visual inspection and/or pressure testing. Therefore the seamless welded and sunk and welded & sunk/plug drawn tubes have the same pressure rating which is superior to that of welded tubing.
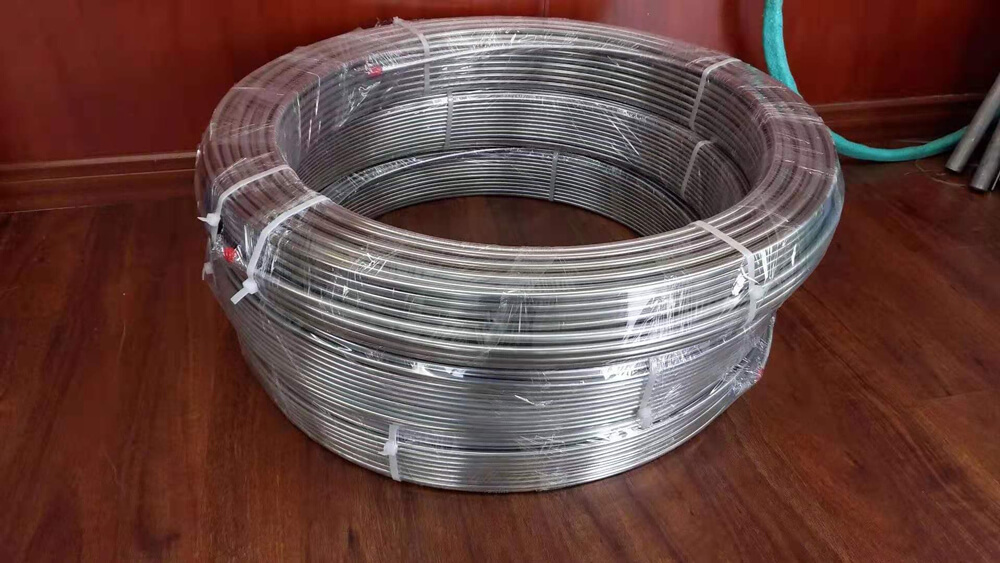